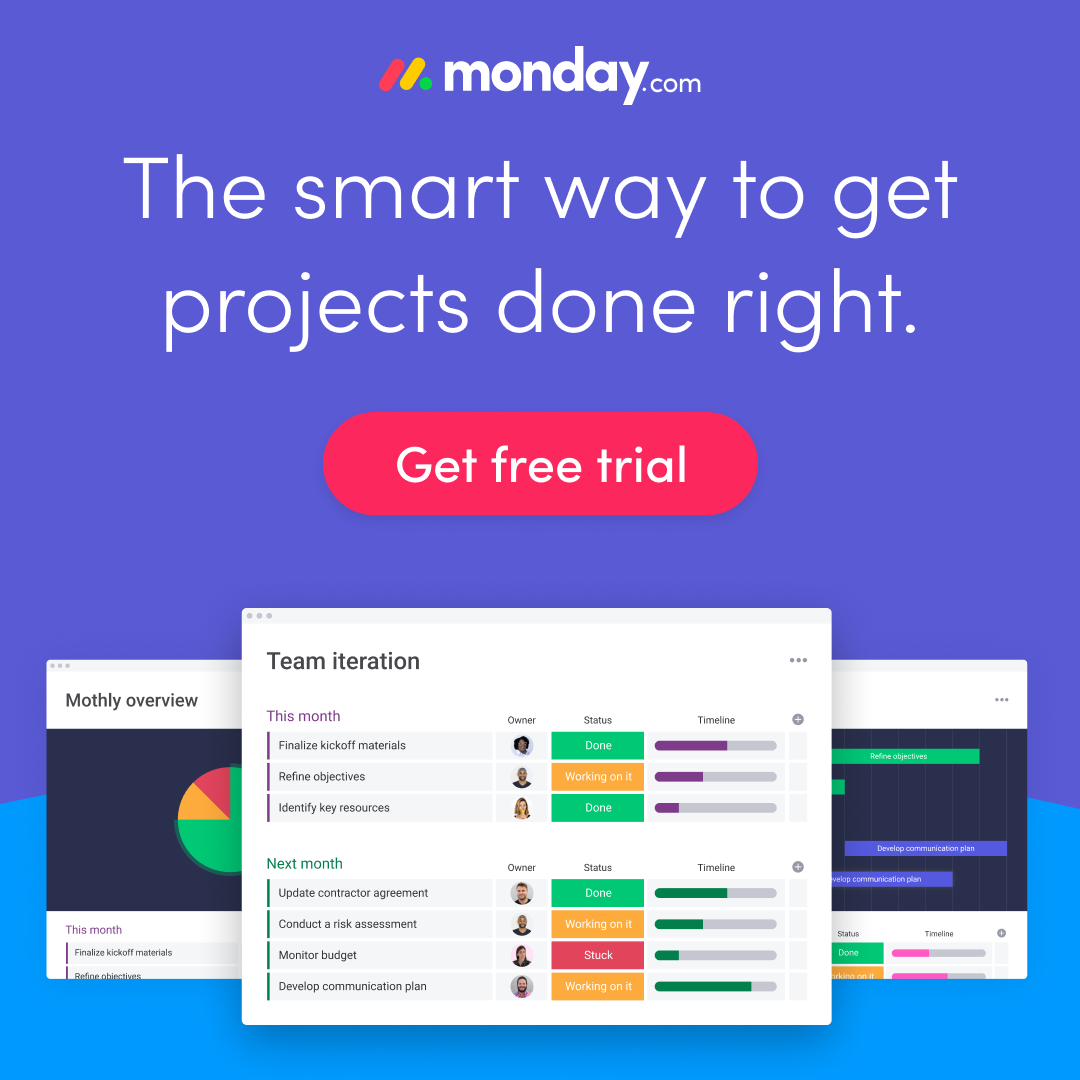
In the dynamic landscape of Information Technology (IT), efficiency and precision are paramount. Amidst the ever-evolving challenges, organizations seek methodologies that can streamline operations while maintaining high standards of quality. This quest for excellence has led many IT firms to embrace Six Sigma methodologies. Six Sigma certification offers a systematic approach to process improvement, focusing on minimizing variability and enhancing efficiency. In this blog post, we delve into the profound impact of Six Sigma in IT processes, exploring how this methodology revolutionizes operations and fosters a culture of continuous improvement.
The introduction of Six Sigma into IT processes marks a paradigm shift in how organizations approach problem-solving and optimization. Initially developed by Motorola in the 1980s, Six Sigma has since gained widespread adoption across industries for its ability to deliver measurable results. In the realm of IT, where precision and reliability are non-negotiable, the principles of Six Sigma resonate profoundly.
Streamlining Processes
One of the core tenets of Six Sigma is the identification and elimination of defects within processes. By applying statistical methods and rigorous analysis, IT teams can pinpoint areas of inefficiency and devise strategies for improvement. Whether it’s reducing software development cycle times or enhancing network reliability, Six Sigma courses empower IT professionals to streamline processes and deliver optimal results.
Enhancing Quality Assurance
Quality assurance is paramount in IT, where even minor errors can have far-reaching consequences. Six Sigma methodologies emphasize the importance of proactive quality management, ensuring that defects are detected and addressed before they impact end-users. Through rigorous testing protocols and continuous monitoring, organizations can uphold stringent quality standards, earning customer trust and loyalty.
Read these articles:
- Six Sigma Certification Training Course Cost in India
- How much does the Lean Six Sigma Certification Cost in Pune?
Optimizing Resource Utilization
In today’s competitive IT landscape, resource optimization is critical for maintaining a competitive edge. Six Sigma provides organizations with the tools and techniques to maximize the utilization of resources, whether it’s human capital, hardware, or software. By identifying inefficiencies and minimizing waste, IT departments can operate more cost-effectively while delivering superior results.
What is Six Sigma
Driving Continuous Improvement
Continuous improvement lies at the heart of Six Sigma philosophy. Through the DMAIC (Define, Measure, Analyze, Improve, Control) framework, organizations are encouraged to embark on a journey of perpetual enhancement. Six Sigma training instills a culture of data-driven decision-making and relentless pursuit of excellence, empowering IT teams to evolve and adapt in response to changing demands. This approach, coupled with the rigorous training provided by a Six Sigma black belt course, ensures that organizations can consistently achieve high-quality outcomes and drive sustainable growth.
Mitigating Risks
In the fast-paced world of IT, risks abound at every turn. Whether it’s cybersecurity threats, system failures, or compliance breaches, organizations must be vigilant in identifying and mitigating potential risks. Six Sigma equips IT professionals with robust risk management tools, enabling them to anticipate threats, implement preventive measures, and swiftly respond to emergencies.
Fostering Collaboration
Effective collaboration is essential for success in IT projects, where interdisciplinary teams must work seamlessly towards common goals. Six Sigma fosters collaboration by providing a common language and framework for problem-solving. Through cross-functional teams and collaborative brainstorming sessions, organizations can harness the collective expertise of their workforce to drive innovation and achieve breakthrough results. This collaboration is further enhanced through Six Sigma Green Belt training, which equips team members with the necessary tools and methodologies to identify and address issues effectively.
Refer to these articles:
- Comparing Scrum and SAFe: A Contrast
- Unlocking Six Sigma Excellence for Operations
- Six Sigma Mastery: Complete Guide
Summary
The integration of Six Sigma principles into IT processes has a transformative impact on organizational performance. By emphasizing process optimization, quality assurance, resource utilization, continuous improvement, risk mitigation, and collaboration, Six Sigma empowers IT teams to excel in an increasingly competitive environment. As technology continues to advance and challenges evolve, organizations that embrace Six Sigma methodologies, supported by Six Sigma training institutes, will remain at the forefront of innovation and efficiency.
What is Quality
Six Sigma Green Belt Introduction
Six Sigma Black Belt Training DMAIC