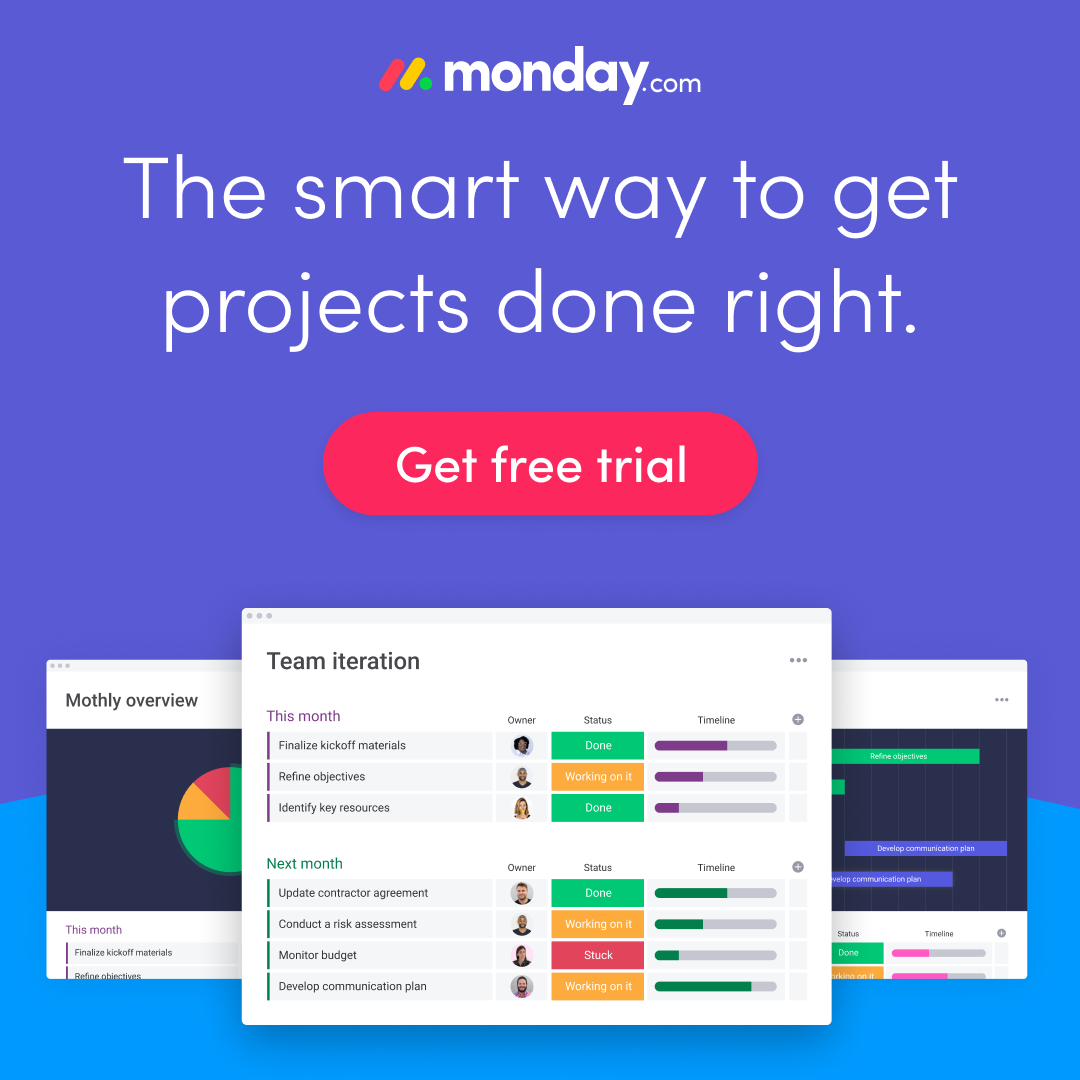
In today’s fiercely competitive business landscape, organizations are continually seeking ways to enhance efficiency, reduce waste, and improve the quality of their products or services. One methodology that has gained widespread recognition for achieving these goals is Lean Six Sigma. Beyond its capacity to optimize processes and boost profitability, Lean Six Sigma has the potential to transform employees into valuable assets. In this article, we will explore how Lean Six Sigma methodologies can empower and elevate employees, making them indispensable contributors to an organization’s success.
Understanding Lean Six Sigma
Lean Six Sigma is a data-driven approach that integrates the principles of Lean and Six Sigma methodologies, often pursued through Six Sigma Certification. Lean focuses on eliminating waste and streamlining processes, while Six Sigma aims to reduce defects and variations in processes. When combined, these two methodologies create a powerful framework for continuous improvement and problem-solving within an organization.
What is Six Sigma
Skill Enhancement
One of the most evident ways Lean Six Sigma transforms employees into valuable assets is through skill enhancement. Employees who undergo Lean Six Sigma training acquire a unique skill set that equips them with the tools to identify, analyze, and solve complex problems within their respective areas of responsibility. These skills, such as data analysis, process mapping, and statistical analysis, are not only valuable within the context of Lean Six Sigma projects but can also be applied to various other tasks and roles within the organization.
Furthermore, Lean Six Sigma, often acquired through the best six sigma training, encourages a culture of continuous learning and development. As employees work on improvement projects, they become adept at setting goals, measuring progress, and adapting strategies, which are all transferable skills that enhance their overall professional growth.
Read these articles:
- How much does the Lean Six Sigma Certification Cost in India
- How much does the Lean Six Sigma Certification Cost in Pune?
Data-Driven Decision Making
In today’s data-driven world, the ability to make informed decisions is crucial. Lean Six Sigma emphasizes data collection, analysis, and interpretation as essential components of the problem-solving process. Employees who have been exposed to Lean Six Sigma principles are more inclined to make decisions based on concrete evidence and facts rather than relying solely on intuition or past experiences.
This shift towards data-driven decision-making, often nurtured through Six Sigma Green Belt courses, not only improves the quality of decisions but also enhances an employee’s credibility within the organization. When colleagues and superiors recognize an individual’s capability to analyze data and make informed choices, their value as an asset to the company increases significantly.
Problem-Solving Skills
Lean Six Sigma is fundamentally about solving problems and improving processes. As employees engage in Lean Six Sigma projects, they gain valuable experience in identifying root causes of issues, brainstorming solutions, implementing changes, and measuring results. These problem-solving skills are not only beneficial within the scope of Lean Six Sigma initiatives but are transferable to various aspects of an employee’s job.
Moreover, employees who excel at problem-solving become sought-after resources within the organization. They are frequently approached to tackle complex challenges, lead cross-functional teams, and drive innovation, all of which contribute to their status as valuable assets.
Collaboration and Communication
Successful Lean Six Sigma projects often involve cross-functional teams working together to achieve a common goal. This collaborative approach fosters teamwork and enhances an employee’s ability to communicate effectively with colleagues from different departments and backgrounds. Lean Six Sigma practitioners learn to navigate through organizational hierarchies, break down silos, and build consensus, which are essential skills in today’s interconnected business environment.
Employees who can bridge communication gaps and facilitate collaboration, often through Six Sigma Courses, become invaluable assets in promoting a culture of teamwork and synergy within the organization. Their ability to bring diverse groups together to solve problems and implement improvements can have a profound impact on an organization’s overall performance.
Results-Oriented Mindset
Lean Six Sigma instils a results-oriented mindset in employees. Through the methodology’s rigorous focus on setting and achieving goals, employees become accustomed to measuring their impact and quantifying the outcomes of their efforts. This results-driven approach not only enhances an employee’s sense of accountability but also aligns their actions with the organization’s strategic objectives.
Employees who consistently deliver results and contribute to the achievement of key performance indicators, often through Six Sigma Training, become highly regarded within their organizations. They are viewed as dependable assets who can be relied upon to drive positive change and achieve desired outcomes.
Refer to these articles:
- Quality Management with Lean Six Sigma Power
- Advantages of Lean Six Sigma Green Belt Certification
- Top 10 Tips for Mastering Lean Six Sigma
Final Note
Lean Six Sigma is not merely a set of tools and methodologies for process improvement; it is a transformative approach that can turn employees into valuable assets, often achieved through Six Sigma Black Belt certification training. Through skill enhancement, data-driven decision-making, problem-solving proficiency, improved collaboration, and a results-oriented mindset, employees who embrace Lean Six Sigma become indispensable contributors to their organizations.
In a world where adaptability and continuous improvement are paramount, Lean Six Sigma equips employees with the knowledge and capabilities needed to thrive and make a lasting impact in their roles. Consequently, Lean Six Sigma, coupled with Six Sigma Black Belt Certification, does indeed have the power to transform employees into invaluable assets for any organization willing to invest in their growth and development.
What is Quality
Six Sigma Green Belt Introduction
Six Sigma Black Belt Training Introduction